Filler masterbatch has been widely used in many different applications, including thermoforming, because of its exceptional advantages. The use of filler masterbatch in thermoforming helps to improve the qualities of the final product while also providing manufacturers with an affordable material choice.
The process of using heat, vacuum, and pressure to transform a plastic sheet into a three-dimensional form is known as thermoforming. Let's take a quick look into filler masterbatch manufacturing before learning about its use in thermoforming. The thermoforming process generally consists of five steps:
Step 1: A thermoplastic sheet is first heated to a malleable, moldable temperature.
Step 2: The procedure of vacuum forming is the second step. wherein the air beneath the mold is suctioned away after the plastic is stretched over a single male mold.
Step 3: The heated plastic is then placed between the male and female molds, which are further pressurized with air at a pressure ranging from 20 to 100 psi to push against the plastic sheet.
Step 4: Afterwards, the plastic object is cooled while maintaining its shape by pumping steam or air into the mold.
Step 5: Lastly, the air is sprayed to release the plastic component that has been molded from the mold.
Compared to other molding techniques, thermoforming is advantageous because of its straightforward technology and great productivity. Among these advantages are:
Cost per quantity: For orders placed in bulk, thermoforming is the best option since it can process a huge number at a fair cost.
Efficiency: Multiple completed parts can be produced from a single material using thermoforming.
Reduced cost design modifications: Thermoforming makes it easy to identify potential fit and design problems early on.
These exceptional advantages make thermoforming the favored method in many industries, including the manufacture of trays, medical packaging, household goods, and more. And now, we will look into the benefits of using filler masterbatch in thermoforming.
Thermoforming is equally compatible with the majority of common resins as other plastic manufacturing techniques, including ABS, HDPE, HIPS, PC, PET, and PVC. However, filler masterbatch was chosen as the best material option in response to the growing need for an affordable material and increasing concerns about the turbulence of the worldwide fossil resin market.
The three primary elements of filler masterbatch, often called calcium carbonate filler, are virgin resins, specialized additives (usually dispersion and processing aid), and CaCO3 powder. The use of filler masterbatch in thermoforming provides various benefits to the final product.
Cost reduction: Because calcium carbonate filler contains CaCO3 powder, which is a reasonable substance, it helps manufacturers reduce their reliance on fossil plastic and partially replaces virgin resins, therefore limiting the negative effects of the global market on entrepreneurs.
Enhancement of characteristics: The use of filler masterbatch in thermoforming results in end products with improved mechanical properties, including printability, dimensional stability, strength, impact strength, and resistance to tearing and friction. The end items perform better and look better as a result of this.
Increasing productivity: The primary ingredient in the filler masterbatch, CaCO3, has strong heat resistance. Thus, adding filler masterbatch in thermoforming lowers processing temperature and shortens the product cycle, resulting in lower energy consumption and higher productivity.
Environmental friendliness: Finally, the environmental safety of calcium carbonate filler is a great benefit. The creation of filler masterbatch is significantly more environmentally benign than that of fossil resin, which has a significant impact on the environment during its manufacturing process. Additionally, it is a perfect substitute for non-renewable resources, allowing thermoforming producers to pursue sustainable development.
3. Common applications of filler masterbatch in thermoforming
Filler masterbatch is a thermoforming material that is frequently used in various applications because of its outstanding advantages.
3.1. Filler masterbatch is used in producing food trays, pots, and covers
Because the filler masterbatch allows the plastic to heat up and cool down more quickly, it significantly increases productivity in thermoforming applications. CaCO3's high heat capacity allows the plastic to melt in the extruder and cool on calendar rolls more rapidly. Less shrinkage and warping follow, giving final goods the precise shape that is needed.
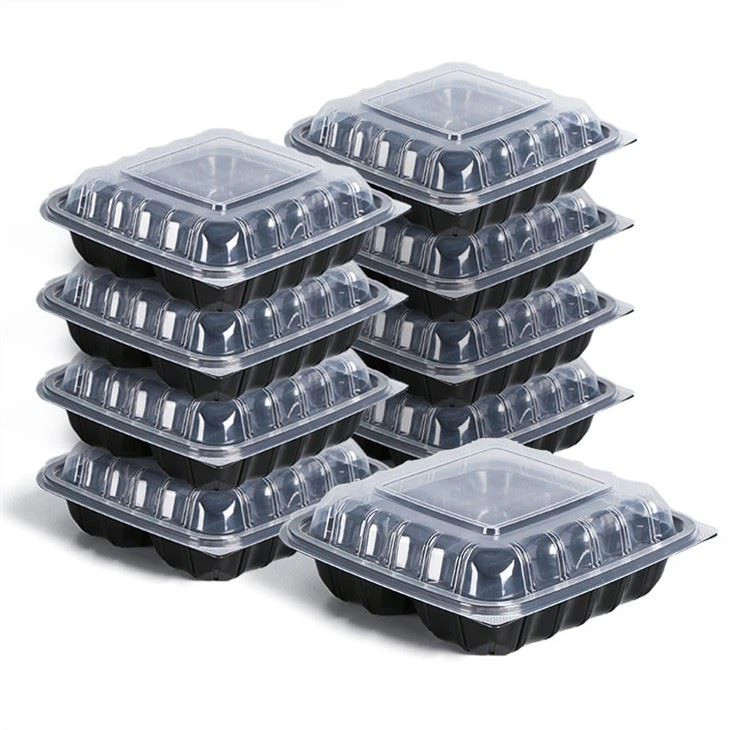
3.2. Filler masterbatch in making refrigerator liners
One of the most popular uses for calcium carbonate fillers is refrigerator liners. Filler can be added to the procedure to greatly improve the final goods' overall performance. A Heritage Plastics study found that calcium carbonate filler can enhance many important characteristics, including dimensional stability, impact strength, and stiffness, at a loading of 18%. As a result, it can precisely satisfy all of the manufacturers' exacting technical specifications.
3.3. Filler masterbatch in transit trays, plastic pallets production
In thermoforming applications with basic designs and high volumes, such as transit trays and plastic pallets, the cost-effectiveness of filler masterbatch is particularly advantageous. Manufacturers can lower the cost of materials by partially substituting virgin resins with filler masterbatch.
3.4. Filler masterbatch in thermoforming- building applications
One of the main industries that uses thermoforming products is the building trade. In the building trade, plastic thermoforming with HIPs (High-impact polystyrene) is frequently used for bath and shower rooms, ducting, fascia panels, underfloor heating systems, and roof vents. As a result, filler masterbatch, which significantly increases efficiency while at the same time reducing material costs, is also an essential component of many applications.
Furthermore, filler masterbatch is used in thermoforming for additional applications like plant pots and seeding trays, home products, disposable cups, and plates,... The components and loading rate of the filler masterbatch will be decided upon based on the specific requirements of each product, ensuring perfect compatibility with final goods.
4. StarPoly produces filler masterbatch in thermoforming
After more than 10 years of development, Starpoly has proven itself as one of the leading producers of filler masterbatch in Vietnam. We have provided a vast range of calcium carbonate fillers, including PP, and PE fillers, to hundreds of customers in more than 60 countries. The usage of our filler masterbatch is primarily attributed to thermoforming.
Recognized for its excellent mechanical properties and cost-effectiveness, StarPoly filler masterbatch is the best option for thermoforming producers seeking a material solution that saves money. Most significantly, our filler masterbatch is made to order according to the specifications of your final goods, reducing the likelihood of unforeseen issues brought on by filler and resin incompatibility.
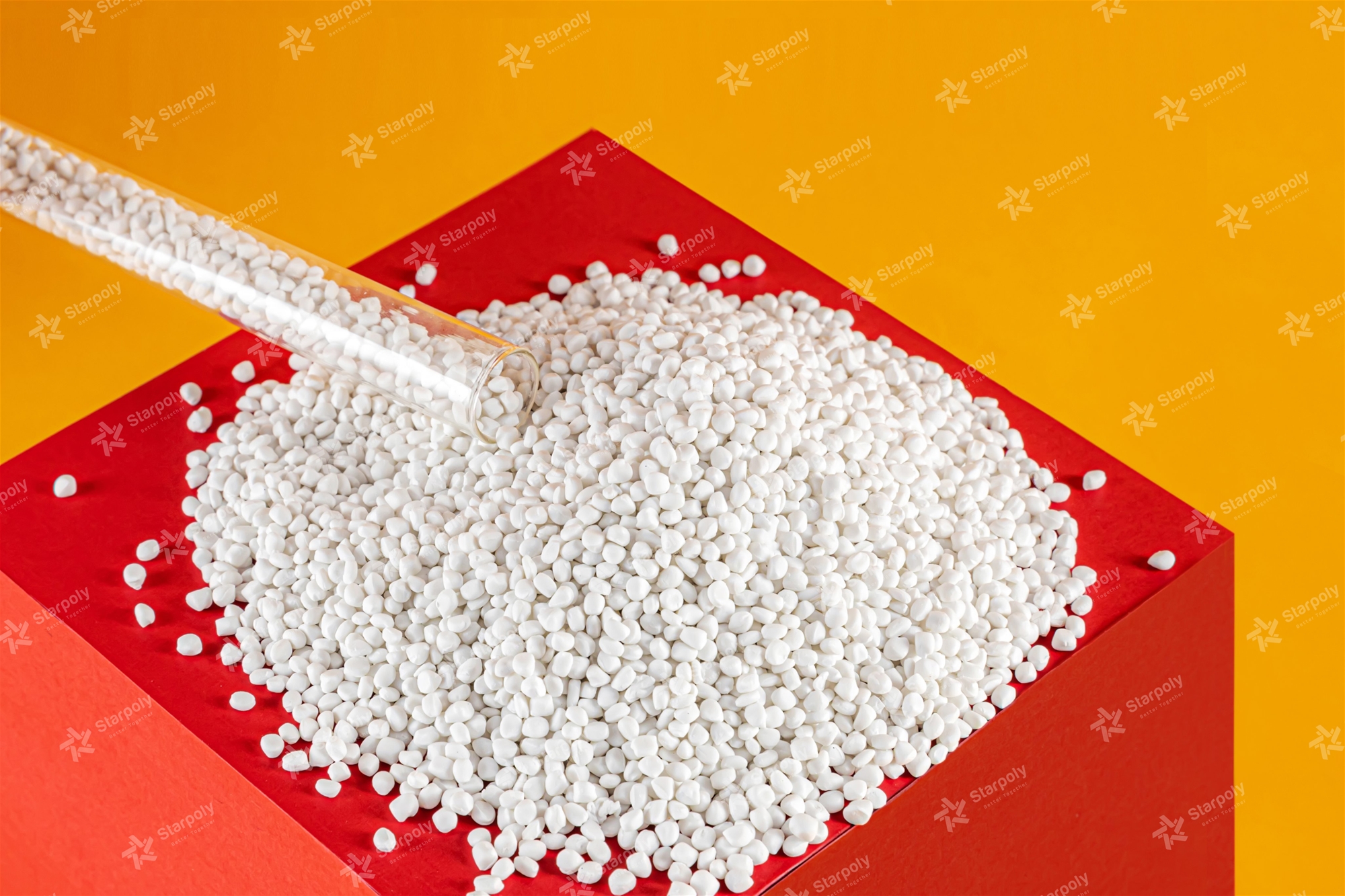
Please get in touch with us if you would like further information.
Contact detail- Alison Taylor (Ms)- StarPoly’s Sales Executive
WhatsApp: +84 82 766 1263
Email: Alison@starpoly.vn/ Sales6.starpoly@gmail.com
Skype: Sales6 StarPoly (Ms Alison)