ADVANTAGES OF USING CALCIUM CARBONATE FILLER IN PP WOVEN PRODUCTION
The utilization of filler masterbatch, particularly PP filler, has seen a significant rise in the past decade. Among the various applications of PP, PP woven products are a significant consumer of PP calcium carbonate fillers. So, what are the advantages that the woven sector gains from using PP fillers? Let's explore this topic in this article.
Polypropylene (PP) is renowned for its impressive mechanical properties, making it a popular choice for numerous applications, including laminated film, household appliance production, and the non-woven and woven industries. However, the reliance on fossil-based materials comes with high costs and environmental uncertainties, which can potentially jeopardize the sustainability of plastic enterprises. This is why the introduction of PP calcium carbonate fillers in the production of PP woven materials is considered.
I. Understanding PP Calcium Carbonate Filler
PP calcium carbonate filler, also referred to as PP filler masterbatch, is a blend of PP resin, calcium carbonate (CaCO3), and additional specialized additives. The appropriate loading rate of PP filler, typically ranging from 15% to 40%, is determined based on the specific requirements of woven applications. The incorporation of common additives such as dispersion agents and processing aids aims to enhance the performance of the final composite during the manufacturing process.
PP filler masterbatch comprises PP resin, calcium carbonate (CaCO3), and other specified additives.
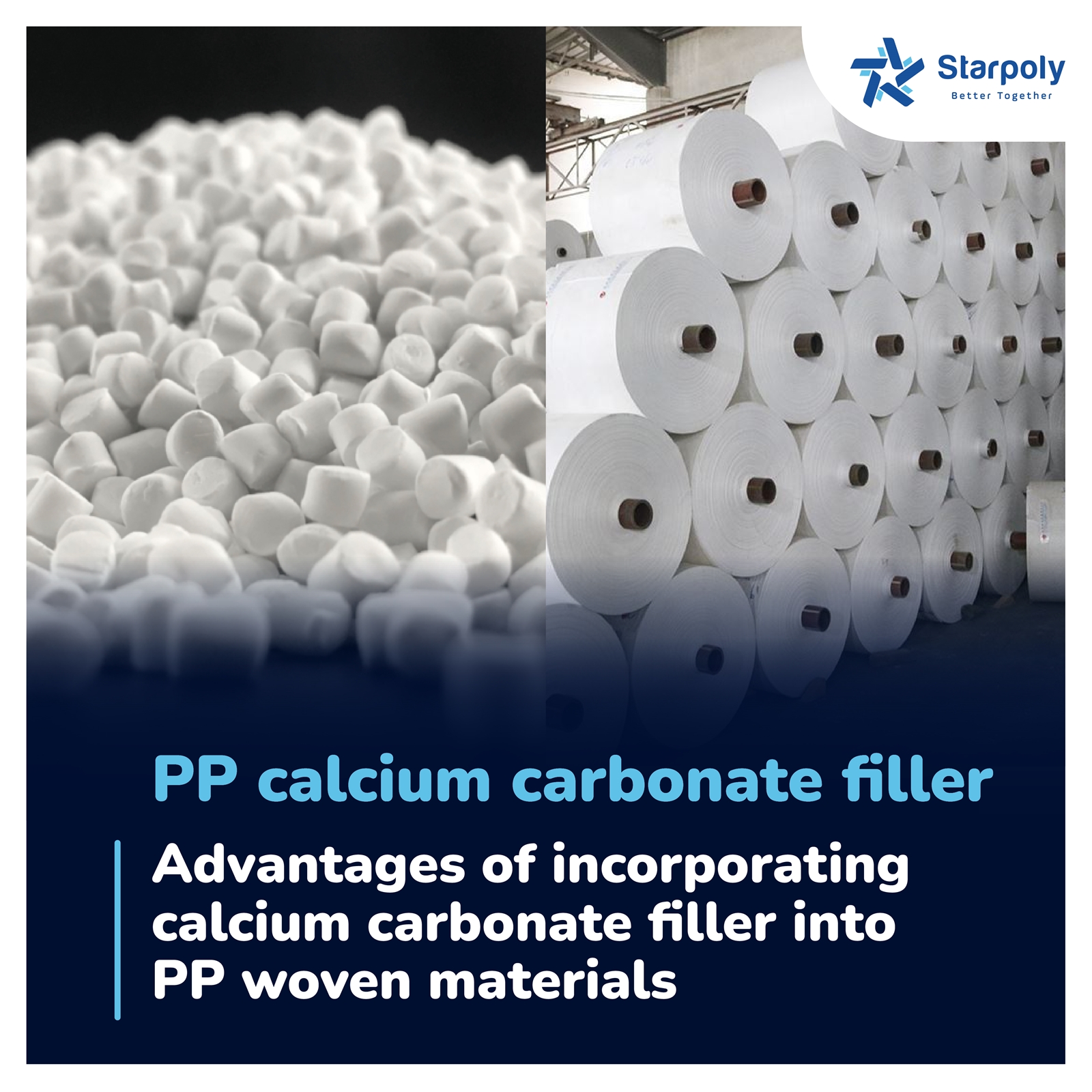
II. What are the advantages of using PP calcium carbonate filler in PP woven production?
Cost Reduction
The key advantage of PP calcium carbonate filler is its primary component, CaCO3, which constitutes up to 70% of its total weight. This reduces the demand for PP resin, leading to a significant reduction in production costs. Additionally, CaCO3 is naturally abundant, offering a more cost-effective and stable alternative to PP resin. Consequently, the utilization of this material effectively reduces production expenses and mitigates the adverse effects of market fluctuations.
Enhancement of Mechanical Properties
Another notable benefit of PP filler is its capacity to improve the mechanical properties of PP woven materials, including flexural strength, impact resistance, and tear resistance. As PP resin is also a component of PP calcium carbonate filler, it seamlessly integrates with existing plastic blends, thereby promoting even dispersion on the surfaces of woven bags. Moreover, PP filler contributes to the stability and shape retention of woven yarn during the manufacturing process.
Increased Productivity
The excellent thermal conductivity of calcium carbonate is a contributing factor to the increased efficiency brought about by PP filler masterbatch. It reduces the time required for each production cycle and conserves a significant amount of energy, ultimately accelerating productivity and overall efficiency. PP filler helps shorten the time required for each product cycle
Enhanced Printability of PP Woven Product
At times, printing on PP woven bags can be challenging due to the inherent surface characteristics. However, the incorporation of PP calcium carbonate filler significantly improves the print quality of your PP woven materials.
5. Reduction in Carbon Footprint
It is undeniable that the plastic industry makes a substantial contribution to environmental pollution due to its extensive use of fossil-based materials. Nevertheless, this issue can be addressed through the adoption of PP filler masterbatch. As calcium carbonate (CaCO3) is a more environmentally friendly option than fossil-based resin, it diminishes the amount of carbon dioxide emissions during the manufacturing process, thereby making a positive contribution to environmental preservation.
III. Maximizing the Effective Use of PP Calcium Carbonate Filler
As previously mentioned, the utilization of PP calcium carbonate filler depends heavily on the technical requirements and manufacturing conditions of PP woven materials. Two primary categories of PP woven products are PP woven sacks/bags (smaller sizes, typically ranging from 10 to 100 kgs) used in various industries such as cement, fertilizer, animal feeds, rice, sugar, grains, and jumbo bags/FIBC (500 kgs and above) designed for container use. To achieve optimal results, plastic manufacturers should take into account the following considerations:

1. Denier (D) is an American measurement unit used to determine the number of grams of yarns in 9000 meters, indicating the fabric's thickness. This parameter provides insights into the type and the required loading rate of filler masterbatch. The thicker the fabric required, the higher the proportion of filler needed. If the anticipated denier is less than 400 and the filler loading rate does not exceed 15%, using PE filler is a better choice, as it enhances yarn elongation and consistency while minimizing yarn breakage.

2. Denier provides insights into the filler masterbatch type and the required loading rate.
2.1. Extruder Speed: The speed of the extruder is a critical factor in determining the filler loading rate. It involves two types of speed during the extrusion phase: the revolution of the screw (rpm) and the operating speed (mpm). Currently, high-speed extruders are gaining popularity as plastic manufacturers aim to enhance productivity.
2.2. Processing Temperature: There are three temperature consideration:
- Extruder Temperature: This is a crucial factor in the production of PP woven materials. The temperature must be sufficiently high to completely liquefy the PP.
Extruder Temperature: It's crucial for the temperature to be sufficiently high to completely liquefy the PP material.
Cool Water Tank Temperature: It has been demonstrated that for achieving optimal impact strength and elongation, yarns should be cooled within the temperature range of 30 to 40 degrees Celsius. Additionally, maintaining a quiet water tank operation is important to minimize vibration, which can lead to yarn inconsistencies.
Heater Temperature: Maintaining the right temperature is key to ensuring consistent yarn shape and preventing the formation of grooves on the yarns.
During the coating/lamination phase, plastic manufacturers can also employ PP filler to reduce production costs and enhance productivity. Some factors to consider include the number of laminated layers, film thickness, and machine speed.
IV. StarPoly PP Calcium Carbonate Filler
StarPoly stands as a prominent manufacturer of filler masterbatch, with our factory situated in Hung Yen, Vietnam. We take immense pride in serving millions of customers across more than 80 countries, offering top-quality filler masterbatches. Our PP filler masterbatch is a meticulously crafted blend of PP resin, calcium carbonate, and specific additives. Its exceptional advantages have earned it widespread utilization in diverse industries, including injection molding, extrusion molding, laminated film production, and woven materials. Among these applications, the use of PP filler has had a transformative impact on woven products, effectively reducing production costs and enhancing numerous properties. Crucially, our calcium carbonate filler can be tailored to meet customers' specific requirements, ensuring it aligns perfectly with your expectations.